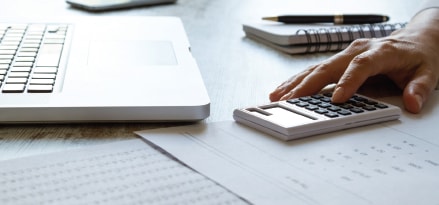
How to calculate savings from conversion to synthetic lubricant
Tom Dietz, Retired Global Industrial Lubricants Technical Manager, ExxonMobil Fuels & Lubricants
When companies switch from a conventional lubricant to a high-performance synthetic, they expect to see a number of benefits related to enhanced safety and improved environmental care. These potential benefits – which can include extended oil drain intervals, enhanced energy efficiency and more reliable equipment performance – may not all be experienced immediately.
That’s why it’s important to know how to properly measure and evaluate lubricant performance and document productivity gains, giving you an accurate picture of your return on investment when it comes to switching to high-performance synthetic lubricants.
When trying to accurately measure the benefits associated with a lubricant change, you must assess the costs and benefits of each lubricant over an equivalent period of time.
Savings over time = (Costs associated with Lubricant A) – (Costs associated with Lubricant B)
Follow the guidelines below to ensure that you are properly calculating the benefits of a lubricant conversion:
Compare apples to apples
When comparing cost of operation with one lubricant to another, always ensure that you are evaluating expenses over an equivalent time period. This consideration is critical to the ultimate assessment, as synthetic lubricants often provide lengthened drain intervals. If one lubricant offers oil drain intervals that are 50 percent longer than the other, you must calculate the costs and benefits of each lubricant technology over the same time in operation to accurately evaluate the performance.
Example: Your comparative assessment for a lubricant offering 50 percent longer drain intervals would reveal three fill and drain intervals with the original lubricant for every two fill and drain intervals of the synthetic.
Assess the investment
When evaluating a lubricant conversion, it is important to recognize that there may be one-time costs associated with converting operations from one lubricant to another, and these costs should be factored into the calculation.
Example: A complete system flushing or cleaning may be required to experience the full benefit of the replacement lubricant. This would be associated with an incremental cost, which will need to be subtracted from the overall savings accrued through conversion.
Be sure to consider the following aspects when totaling associated costs:
- Price of lubricant and consumables: Total the cost of lubricant in operation using the delivered pricing of each product to your plant site. Be sure to evaluate the cost of the two lubricants based on the same packaging style, when appropriate. Additionally, capture the cost associated with consumable parts, such as filters.
- Price of disposal: Capture the cost of disposal for the used lubricant over equal time for each trial and include in the total cost of operation.
- Price of labor: Often, switching to a synthetic lubricant will reduce the amount of labor associated with routine maintenance, as fewer oil drains translate to less time spent changing oil. A reduced cost of labor will translate to a credit toward the overall cost of conversion to a synthetic.
Evaluate overall energy consumption
The difference in energy consumption required to power an application will vary between lubricant technologies. Differences in energy efficiencies of lubricants can be small – often smaller than 3 percent – making it challenging to determine the overall cost of energy in a particular application. It will be necessary to ensure you are capturing these values in controlled environments, taking care to maintain ambient temperature and humidity conditions throughout the test.
In laboratory testing, we generally run efficiency tests multiple times and compare the outcome values to determine if there is a variance between trials. If the results of the second test of the same lubricant are significantly different than those of the first, additional data may be required to understand overall energy consumption of the two lubricants.
If energy consumption is reduced, then emissions have likely diminished proportionally, potentially resulting in associated credits. At Imperial, we currently assess the value of emissions reductions using an estimate of CAD $40 for each reduced ton of CO2.
Hopefully, by using the above methods, you will be able to demonstrate similar advantages of a lubricant conversion at your site. Consult with your Mobil™ Field Engineering Services representative for help with your evaluations.